Corporate Report 2024: Letter from the Management Board | About This Report | Sustainability Management | Corporate Bodies and Management | Report of the Supervisory Board | Turn Challenges into Opportunities | Group Management Report | Products | Safety and Health | Environment | People | Social Commitment | Consolidated Financial Statements (condensed version) | Multi-Year Overview | Global Compact: Communication on Progress (COP) | ALTANA worldwide | List of Shareholdings | Overview | Contact
Innovation
As a specialty chemicals company, innovations are an important factor for ALTANA, enabling us to offer our customers new, competitive solutions and at the same time to meet current requirements regarding performance profile, costs, environmental protection, and sustainability. Thanks to close cooperation with our customers, we are able to identify global technology trends at an early stage and to be immediately involved in new development fields. This enables us to develop tailored solutions quickly and reliably. We build on existing competencies, on the one hand, and gain access to new ones on the other, to continuously adapt our product portfolio to market and customer needs. There is also great potential to combine our competencies across the divisions to establish innovative solutions on the market more quickly and efficiently. To this end, our research and development teams have access to the latest analytical methods in our chemical laboratories and application-technology test laboratories. Numerous awards from our customers underscore our success as an innovative solutions provider.
In addition to the activities in the divisions, selected innovations are initiated and coordinated at the ALTANA level to explore new business areas and address emerging technological and market trends. These innovations are built upon the strong competencies of the divisions across the entire value chain, as well as the synergies that emerge between them. To create new areas of innovation, we employ a variety of complementary approaches, including the ALTANA Institute, our technology platforms, corporate venturing, and other innovative growth fields.
With the help of the ALTANA Institute, we leverage external networks and foster close cooperation with universities and research institutes around the world to gain valuable external insights for our development. In this area, we collaborate on fundamental research, which serves as the foundation for more application-oriented internal research and development activities. Completed projects are transferred to our business divisions through technology transfer. This year, seven new projects were launched, further strengthening our partnerships. We expanded our longstanding collaboration with Niederrhein University of Applied Sciences on two topics and initiated a new project with the University of Bayreuth. Additionally, our strategic partnership with Friedrich Schiller University Jena was enhanced with two more projects. A new research collaboration was also established with Graz University of Technology in Austria. For the first time, a doctoral thesis is being conducted at the ALTANA Institute in partnership with the University of Twente, Netherlands.
ALTANA’s investments in technology platforms saw a significant increase compared to the previous year, highlighting the ongoing expansion of the division, driven by strategic customer collaborations.
The “Printed Electronics” technology platform, integrated into the ELANTAS division, significantly ramped up its marketing activities during the reporting period and expanded its reach to additional regions. Sales grew due to new business opportunities and an expanded product portfolio, while the project pipeline continued to grow.
As part of the “Cubic Ink” technology platform, the product portfolios for both inkjet and VAT polymerization were standardized and completed. The first major order was secured for applications in dental medicine, with additional projects pending final approval.
The “Heliosonic” laser transfer technology platform was able to sell another print head and put it into operation at the customer’s premises. In addition, a printing machine with a larger print width was successfully built and accepted.
Thanks to the close collaboration between the Corporate Innovation and Corporate Venturing departments, ALTANA is able to continuously assess technology and market potential, entering new attractive markets through targeted investments in innovative technology companies. For instance, in the 2024 fiscal year, ALTANA initiated a partnership with the newly affiliated Nordtreat Group to jointly develop bio-based flame retardant additives.
A growth field project in the hydrogen sector was initiated to develop profitable new business with strong growth potential. The goal is to further expand existing expertise and create innovative solutions for the production, transportation, and storage of hydrogen.
The basis for our innovative strength is an open and dynamic corporate culture that gives our 1,294 employees worldwide in our research and development centers the freedom to act creatively and entrepreneurially. The equipment in our development centers enables our employees to turn their ideas into market-ready solutions. Compared to the previous year (€ 196.5 million), our research and development expenditure increased by € 16.8 million to € 213.3 million. The decline in the proportion of sales accounted for by research and development expenses to 6.7 % (previous year: 7.2 %) is primarily due to the significant increase in sales compared to the previous year. In general, our expenditure is linked to the achievement of important milestones, the implementation of individual customer requirements in future, innovative products, and the long-term orientation of our innovation activities.
Employees
At the end of 2024, the companies of the ALTANA Group employed 8,382 people worldwide (previous year: 7,939). This represents an overall increase of 443 employees, or 6 %. The primary driver of this growth was the acquisition of the Silberline Group in January 2024, which contributed 430 employees.
In the BYK division, the workforce grew by 77, reaching a total of 2,592 employees in 2024 (previous year: 2,515). The increase in employees was seen across all functional areas, with particular growth in administration, research and development, and production.
The number of employees at ECKART increased by 389, reaching 2,100 by the end of 2024 (previous year: 1,711). The acquisition of the Silberline Group added 430 employees, with 70 % of them working in production. Excluding the Silberline acquisition, the number of employees in the ECKART division declined, particularly in research and development and administration, while there was a slight increase in production.
In the ELANTAS division, staff numbers decreased by 60, bringing the total to 2,041 in 2024 (previous year: 2,101). This reduction was primarily due to integration measures following the Von Roll acquisition. The decline affected not only production but also other functional areas.
ACTEGA’s workforce increased by 21, reaching a total of 1,375 employees in 2024 (previous year: 1,354). The growth in the ACTEGA division was primarily seen in the areas of production and administration.
The headcount at the Group holding companies rose by 16 to 274 in the past fiscal year (previous year: 258). At 12 people, a large part of the increase was attributable to ALTANA Management Services GmbH (AMS), which provides both global and regional services for Group companies.
The functional structure of the workforce changed only slightly in the 2024 fiscal year due to the acquisition of the Silberline Group. The share of employees in production increased to 54 %, or 4,546 people (previous year: 4,270), with 298 of these employees coming from the acquisition of the Silberline Group. The number of employees in research and development rose by 29 to 1,294 in 2024 (up from 1,265), with 40 of these additions from the Silberline Group. In marketing and sales, the employee count grew by 36, reaching 1,303 in 2024 (up from 1,267), with all 36 new employees coming from the Silberline Group. The administration department included 1,239 employees in the reporting year (previous year: 1,138), with an increase of 101 employees, 56 of whom were taken over from the Silberline Group.
In terms of regional structure, there were only slight shifts from Europe to Asia in 2024 compared to the previous year. European Group companies continued to account for the largest share of the workforce, with 5,181 employees (previous year: 5,091). At the end of the year, 3,873 employees (up from 3,847) were based in Germany, with the majority working at the largest production and development sites of the ECKART and BYK divisions in Hartenstein and Wesel, respectively. The inclusion of the Silberline companies led to an increase of 87 employees in the UK. In the Americas, the number of employees rose by 135 to 1,944 by the end of 2024 (previous year: 1,809), with the increase mainly attributed to the American company of the Silberline Group, which added 123 employees. The workforce in Asia grew by 218 employees, from 1,039 in the previous year to 1,257 in 2024. The newly acquired Asian Silberline companies accounted for 215 of these new employees, with the largest share, 206, based in China.
At the end of the 2024 fiscal year, 2,155 women and 6,227 men worked at ALTANA. 90 % of all employees had an unlimited contract and 10 % a limited contract on the balance sheet date. At the end of 2024, 76 % of female employees were employed full-time and 24 % part-time. Among male employees, the share of full-time employees was 97 %. Apart from the Group’s own employees, 453 people from employment agencies worked for Group companies as of December 31, 2024. The increase compared to the previous year (+ 384) is primarily due to a high number of temporary workers at Von Roll (308), the majority of whom are again attributable to Von Roll India (287).
In the year under review, the focus of the Human Resources department was on implementing new initiatives and expanding established processes and systems across other ALTANA companies. These measures align with the division’s strategic goal of enhancing its attractiveness as an employer and fostering a corporate culture based on diversity, equality, and inclusion. Additionally, these efforts ensure that our employees have access to attractive and appropriate training opportunities.
To enhance our attractiveness as an employer, surveys were conducted among our employees. Since January 1, 2024 the offer of a supplementary bicycle leasing service as part of a deferred compensation scheme for employees in Germany has not only fulfilled a frequently expressed wish, but also promotes health through physical activity. The foundation for this was laid in 2023 with the conclusion of a collective agreement between the IGBCE trade union and the German Chemical Employers’ Association (BAVC).
A significant step in the continuous expansion and improvement of further training opportunities was taken in 2024 with the launch of the Wise Peers Initiative. This program is specifically designed for employees with more than 20 years of professional experience within the Group. As part of this training and activation program, key topics such as knowledge transfer, lifelong learning, and appreciation were covered.
In addition to implementing additional benefits and further training opportunities, the focus was also placed on further harmonization and increasing efficiency. As part of integrating the individual companies of the former Silberline Group into the existing corporate structures of the ECKART division and the ALTANA Group, the portfolio of additional benefits for employees of Silberline Inc. was aligned with the offerings of other U.S.-based companies. This adjustment will simplify local personnel processes moving forward, without significantly reducing the range of benefits provided to employees. For several years, all ALTANA companies in the U.S. have been managed and billed by a common payroll provider. Starting in January 2025, Silberline Inc. will also be serviced by this provider, streamlining future cooperation. This harmonization is an important step in preparing Silberline for integration into SAP SuccessFactors and other IT systems in the coming year.
In the reporting year, the compensation review process was extended to other Group companies via SAP SuccessFactors, increasing the efficiency and transparency of the process. Further implementations are planned for 2025.
Environment and Safety
Environmentally compatible management and occupational safety are key components of ALTANA’s corporate strategy. The ALTANA Group measures progress in environmental protection using specific key figures, such as the consumption of natural gas or electricity as energy sources and the resulting greenhouse gas emissions, and in the area of safety with the help of accident figures. Our aim here is to continuously reduce the number of accidents, ideally to zero.
In terms of environmental protection, our goal is to continuously reduce energy consumption at all our sites and in all areas and to promote the use of energy from renewable sources. Since 2020, the global purchase of green electricity has marked a key milestone on our path to independence from fossil fuels. The sites also invest in energy transformation measures annually.
At the end of September 2023, the ELANTAS division acquired a majority stake in the Swiss Von Roll Group. In January 2024, the ECKART division acquired the Silberline Group. The data from all sites of the newly acquired companies will be fully integrated into the existing reporting system from 2024.
The issue of safety is a top priority at ALTANA. ALTANA ensures continuous improvement in the safety of its employees by means of various technical and organizational measures tailored to the production conditions at the sites and to the laws and regulations that apply there. All our worldwide sites have established their own safety organization, which is responsible, among other things, for complying with all local occupational safety regulations, for training and education measures, and for recording and evaluating accidents. Throughout the Group, the Work Accident Indicator (WAI) serves as the key performance indicator for recording and evaluating the development of occupational safety at all sites based on reported accidents with lost days. Three key figures are defined for better comparability: WAI 1 refers to the number of reported occupational accidents with lost work time of one day or more per million working hours. WAI 2 comprises the number of reported occupational accidents with lost work time of more than three days per million working hours. And WAI 3 represents the number of lost work days due to reported occupational accidents per million working hours.
ALTANA determines the working hours on the basis of the actual hours worked. If such recording is not possible, a qualified estimate of the average hours worked is made. Accidents are recorded directly on site and reported to a defined group of persons within 48 hours. On a quarterly basis, the reported accidents with lost work days are evaluated in a global IT system. Subsequently, the evaluations are made available to all responsible persons, such as the Management Board, division presidents, managing directors, and experts from the area of Environment, Health and Safety (EH&S). On the basis of this data, ALTANA’s Management Board, together with the EH&S department, sets target values for the three WAIs for each year, which apply equally to all ALTANA Group companies.
For 2024, ALTANA again defined ambitious target ranges for all three accident indicators (WAI 1: 0 to 2.3; WAI 2: 0 to 1.5, and WAI 3: 0 to 27.0), once again emphasizing how important the continuous improvement of occupational safety is for the company. These target values did not yet include the newly acquired companies, partly because their safety cultures were at different levels of maturity. ALTANA’s goal is to bring these new sites up to the safety standards of the existing companies within the next three years. To ensure this goal is met, ALTANA will report two sets of WAI key figures moving forward and establish differentiated target ranges.
Including the newly acquired companies, the number of accidents has increased. However, if we look at the number of occupational accidents excluding acquisitions, we succeeded in significantly reducing the figures compared to the previous year and achieving the respective target ranges. Globally, 41 accidents with days lost were reported at ALTANA. Of these, 20 accidents are attributable to the newly acquired companies. Overall (including the acquisitions), 10 more accidents were registered compared to the previous year. Based on the hours worked, the following WAI values result, adjusted for the acquisitions: WAI 1: 1.9 (previous year: 2.8); WAI 2: 1.1 (previous year: 1.7), and WAI 3: 21.5 (previous year: 31.8). Including the newly acquired companies, the WAI values are as follows: WAI 1: 2.8; WAI 2: 1.9; WAI 3: 35.9.
ALTANA has also been addressing the issue of energy efficiency and the associated greenhouse gas emissions for several years. In addition to absolute values, energy consumption is set in relation to the quantity of finished goods that are produced. ALTANA establishes annual reduction targets for energy consumption in relation to the quantity of produced finished goods. The recording and calculation of emissions relates, as Scope 1, to direct greenhouse gas emissions from emission sources owned or controlled by the Group. These include, for example, the combustion of primary energy sources in the course of heat generation and fuel consumption in the company’s own vehicle fleet at some sites. Scope 2 includes indirect greenhouse gas emissions from the performance-related purchase of electricity. They are recorded and calculated in accordance with the standard “A Corporate Accounting and Reporting Standard – Revised Edition” of the Greenhouse Gas Protocol initiative. The energy consumption of all production sites included in the scope of consolidation is recorded and evaluated in a global reporting system. The CO2 equivalents for Scope 2 are calculated based on conversion factors (g CO2/kWh) defined by the International Energy Agency (IEA) in line with the currently published values (2022) for the location-based method and with the aid of emission factors of the electricity supplier or an individual electricity product for the market-based method. For Scope 1, we use the conversion factors from the Intergovernmental Panel on Climate Change (IPCC).
The companies generally determine consumption based on utility bills. If this is not possible for the last two months of the reporting year, the companies first make a qualified estimate of the values. As a result, the previous year’s figure may be adjusted retrospectively in the following year as soon as all invoices are available. In 2024, ALTANA had a total energy consumption of 871,320 MWh (previous year: 611,843 MWh). The main energy sources were natural gas (467,990 MWh) and electricity (321,599 MWh). ALTANA set a target value of 1.17 MWh/t for the specific energy parameter – based on one ton of finished goods – for 2024 and slightly exceeded this with 1.19 MWh/t (previous year: 1.18 MWh/t) for the ALTANA Group excluding acquisitions. Including the acquired companies of the Von Roll Group and the Silberline Group, this results in a specific energy value of 1.50 MWh/t. The significantly higher value is due to the different product portfolio and the more energy-intensive manufacturing processes. The resulting greenhouse gas emissions are listed in the tables further on.
For the purchased electricity of 321,599 MWh, the same amount of Guarantees of Origin was acquired in accordance with recognized quality standards (for example, CoO for Europe, GREEN-E for the U.S., and IREC for China) and through a German PPA (Power Purchase Agreement). This is electricity that is generated from renewable energies and whose origin is made transparent by means of a Guarantee of Origin. ALTANA plans to finalize the decommissioning of these Guarantees of Origin for 2024 in April 2025. According to the location-based method, 113,751 tons of CO2 equivalents are calculated for this electricity procurement, but this corresponds to zero CO2 emissions due to the measures taken by ALTANA according to the market-based method, as described above. The purchase of steam, district heating, and compressed air causes 1,880 tons of CO2 equivalents in Scope 2 greenhouse gas emissions according to the location-based method and the market-based method.
In 2024, ALTANA successfully had long-term and short-term targets for the reduction of greenhouse gas emissions validated by the Science Based Targets initiative (SBTi). These targets include the reduction of emissions in Scopes 1, 2, and 3. To meet the requirements of the GHG Protocol and the SBTi, the greenhouse gas emissions of our acquisitions of Von Roll, Silberline, and Imaginant were also retroactively included in these calculations. These adjustments are based partly on projections and partly on actual data. The recalculated greenhouse gas emissions (Scope 1 and 2) for 2021, which serves as the base year for SBTi, and for 2023 including the acquisitions (adjusted) are compared with the values reported from previous years in the following table.
As part of the SBTi initiative, ALTANA has set both short-term and long-term emission reduction targets. By 2032, emissions in Scope 1 and 2 are to be reduced by 50 % compared to the base year, with a further reduction of 90 % targeted by 2040. To track progress toward these goals, ALTANA reports its Scope 1 and 2 emissions annually, along with the interim target that must be met according to the SBTi pathway to stay within the greenhouse gas budget aligned with the Paris climate targets. The following table presents ALTANA’s Scope 1 and 2 emissions in comparison to the base year and the interim target.
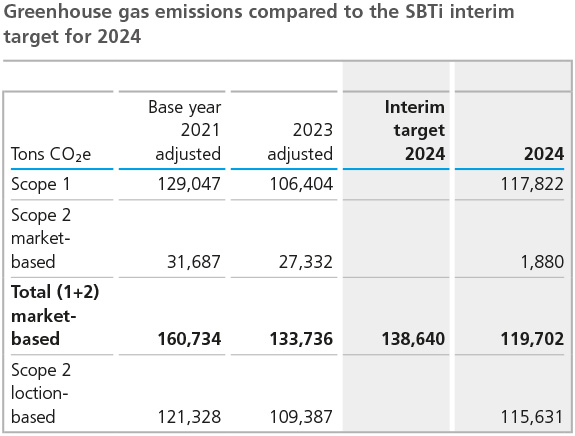
As the table shows, the annual interim target for Scope 1 and 2 emissions was achieved in 2024, reaffirming the ALTANA Group’s commitment to its climate strategy through various measures and projects. In addition to focusing on reducing emissions within its own value chain, ALTANA also invests in certified climate protection projects. When selecting these projects, we ensure they are certified according to internationally recognized standards such as the Verified Carbon Standard (VCS) and contribute to selected United Nations Sustainable Development Goals. Furthermore, we review the portfolio annually to assess whether it continues to meet our requirements. For the reporting period, ALTANA offset 103,300 tons of CO2 equivalents through certificates from the Kinnaur hydropower plant project on the Satluj River in the Himachal Pradesh region of India (Verra Register VCU serial number 9355-83857819-83961118-VCS-VCU-997-VER-IN-1-1742-01012018-31122018-0). This quantity corresponds to approximately 88 % of the greenhouse gas emissions generated in Scope 1 during the reporting year.
This voluntary contribution to mitigating climate change is not offset against the emissions generated. However, the approach aligns with the SBTi’s best practice recommendations for support measures on the path to decarbonization. ALTANA has set the goal of voluntarily offsetting as many CO2 equivalents as the company generates in Scope 1, Scope 2, and selected categories of Scope 3 starting in 2025.