Letter from the Management Board | About This Report | Sustainability Management | Corporate Bodies and Management | Report of the Supervisory Board | Climate Protection at ALTANA | Group Management Report | Products | Safety and Health | Environment | Human Resources | Social Commitment | Consolidated Financial Statements (condensed version) | Multi-Year Overview | Global Compact: Communication on Progress (COP) | ALTANA worldwide | List of Full Ownership | Overview - About This Report | Contact
Team spirit and technology lead
to a carbon-free site
At the BYK plant in Wesel, a new system has ensured more efficient processes and the resulting saving of valuable resources for some time now. The installation exemplifies the ALTANA Group’s path to climate neutrality – everywhere in the world.
The 38-year-old played a significant role in the simultaneous achievement of two sustainability-relevant goals: lower energy requirements for the site’s heat supply and purified exhaust air with lower greenhouse gas emissions.
Heiko Moritz has reason to be satisfied. The 38-year-old, who works as an Operations and Planning Engineer at the BYK plant in Wesel, has played a significant role in achieving two sustainability-related goals at the same time: lower energy requirements for the site’s heat supply and purified exhaust air with lower greenhouse gas emissions and the related positive effect on the environment. As a result, Moritz and his team are implementing something that ALTANA as a Group is committed to worldwide: a significant reduction in natural gas consumption as a major step toward zero carbon sites. ALTANA aims to be climate neutral worldwide by 2025.
Conversion of exhaust gas cleaning and heating of heat transfer oil
At the BYK plant in Wesel, it was about the conversion of the thermal afterburning system. This system converted process exhaust air into CO2 and water vapor. In addition, the plant was used to heat so-called thermal oil, which is deployed for heating in the plant. The problem: The energy efficiency was only around 85 percent and thus behind today’s technical possibilities.
As the responsible engineer, Heiko Moritz was tasked with finding a sustainable replacement for the existing afterburning plant. The team around the engineer examined various options up to and including a complete rebuild of the existing plant. It quickly became clear that the strongest effects could be achieved by decoupling heat generation and exhaust gas cleaning. In the future, special scrubbers should ensure clean air. But many tasks had to be performed in the course of the changeover, which would put too great a strain on a single team. For the trial operation in several pilot plants alone, measured values had to be collected and evaluated to ensure compliance with all environmental specifications. Good teamwork was an essential key to success. The measurement data was collected using in-house measurement technology, while the analytics department carried out the evaluation.
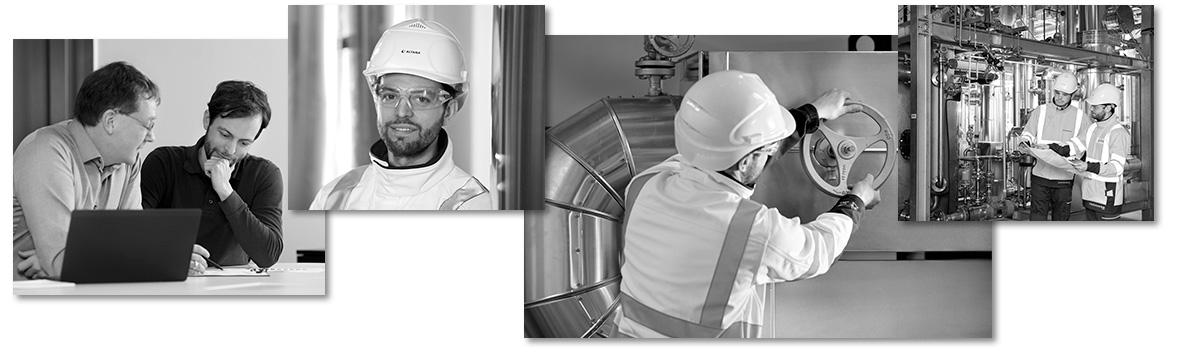
Planning Engineer Heiko Moritz and his team examined various options in their quest to find a sustainable replacement for the existing thermal afterburning system at the Wesel site. | Many tasks had to be mastered during the changeover. Good teamwork was an essential key to success, because the replacement took place during ongoing operations.
Replacement during operation
The replacement was akin to open-heart surgery because operations had to continue. This, too, was possible only thanks to a great team effort. “Everyone worked hand in hand. We don’t just talk about climate protection, but implement it step by step as a team,” says Heiko Moritz. The result speaks for itself: Heat loss could be reduced by two thirds. In addition, the now separate heat generation occurs with a ten-percent improved efficiency, which is now up to 95 percent. This effect gives rise to a considerable reduction in natural gas consumption, thus reducing greenhouse gas emissions by around 400 tons per year. It is not only the company that benefits from the new plant, by achieving savings and improving its carbon footprint. The area surrounding the BYK plant can also look forward to even better exhaust gas values. Last but not least, there is Heiko Moritz himself, who lives in Wesel with his young family. “It’s nice to be able to experience the effect of your own work so directly – especially if you like to be hands-on and put your money where your mouth is, for the benefit of future generations. The experience gained from the retrofit project was so inspiring that now, as a Planning Engineer, I’m already looking forward to the next project on our way to becoming a carbon-free site,” he concludes.